Geodyn Solutions: Enhanced Tilapia and Shrimp Feed Manufacturing Facility Proposal for the Dominican Republic
Executive Summary
Geodyn Solutions proposes an enhanced, scaled-up aquaculture feed manufacturing facility in the Dominican Republic to produce 150,000 tons of premium feed annually for tilapia and shrimp, targeting export markets in North America, South America, and the Caribbean. Building on the $75 million facility (artifact_id: 2fddf9a7-fbba-4684-a97c-d613660de114) and incorporating recommended ingredient enhancements (artifact_id: a3e7b9c2-4c7d-4f9e-9b0a-5f6e8b7c3d4a), this $76 million project (including 20% contingency) integrates black soldier fly (BSF) larvae, silkworm pupae, algae (Spirulina, Schizochytrium sp., Chlorella vulgaris), soybean meal, fermented cassava meal, moringa leaf powder, yeast hydrolysate, probiotic microbes, prebiotics, and clear water microbiology technologies. The facility supports the $50 million tilapia and shrimp farm (artifact_id: 756c712f-8137-4b35-aa34-862f0af7c8a6), optimizing cost efficiency, sustainability, and export potential. With a projected ROI of 115.8%, 810 jobs, and $220 million in annual export revenue, this initiative positions the Dominican Republic as a global leader in sustainable aquaculture feed production.
Project Overview
The enhanced facility scales production to 150,000 tons/year (120,000 tons tilapia feed, 30,000 tons shrimp feed), with 50,000 tons supporting the integrated farm and 100,000 tons for export. Located near Samaná Peninsula, it leverages the Dominican Republic’s warm climate, abundant resources, and port access (Puerto Plata, Santo Domingo) to meet growing demand for sustainable, nutrient-dense feed. The addition of fermented cassava meal, moringa leaf powder, Chlorella vulgaris, and yeast hydrolysate improves feed quality, feed conversion ratio (FCR), animal health, and market appeal, enhancing ROI and export competitiveness.
Rationale for Enhancements
The enhanced feed formulation addresses:
- Export Market Demand: Premium, sustainable feed with improved FCR and health benefits commands 10-20% higher prices in North America (80% import-dependent), South America (6% annual aquaculture growth), and the Caribbean.
- Nutritional Optimization: New ingredients boost protein, minerals, and immunity, reducing mortality and antibiotic use.
- Cost Efficiency: Local sourcing of cassava, moringa, and yeast hydrolysate lowers costs; improved FCR reduces feed use.
- Sustainability: Byproducts and wastewater use align with circular economy principles, enhancing environmental credentials.
- Economic Impact: Increased production and premium pricing triple job creation and export revenue, supporting national development goals.
Enhanced Feed Formulations
The formulations incorporate recommended ingredients to meet tilapia (35% protein, 8% fat) and shrimp (40% protein, 10% fat) requirements, improving FCR and export appeal.
- Tilapia Feed:
- 25% BSF larvae (40-45% protein, cost: $2,000/ton)
- 20% silkworm pupae (50-60% protein, $2,500/ton)
- 12% Spirulina (60-70% protein, $3,000/ton)
- 5% Schizochytrium sp. (20% protein, 50% DHA, $4,000/ton)
- 5% Chlorella vulgaris (50-60% protein, $3,500/ton)
- 10% fermented cassava meal (5-10% protein, $300/ton)
- 3% moringa leaf powder (25-30% protein, $1,500/ton)
- 10% soybean meal (44-48% protein, $500/ton)
- 2% yeast hydrolysate (40-50% protein, $1,000/ton)
- 3% probiotics/prebiotics ($70/ton)
- 2% vitamins/minerals
- Nutritional Profile: 35% protein, 8% fat, FCR ~1.14 (vs. 1.2-1.4).
- Cost per Ton: $1,400 (vs. $1,300 original).
- Shrimp Feed:
- 20% BSF larvae
- 15% silkworm pupae
- 12% Spirulina
- 10% Schizochytrium sp.
- 5% Chlorella vulgaris
- 8% fermented cassava meal
- 2% moringa leaf powder
- 12% soybean meal
- 3% yeast hydrolysate
- 3% probiotics/prebiotics
- 2% vitamins/minerals
- Nutritional Profile: 40% protein, 10% fat, FCR ~1.14 (vs. 1.2).
- Cost per Ton: $1,650 (vs. $1,500 original).
Probiotic Microbes, Prebiotics, and Clear Water Microbiology
- Probiotic Microbes:
- Description: Bacillus subtilis, Lactobacillus plantarum, Saccharomyces cerevisiae (10^8 CFU/g) enhance gut health, nutrient absorption, and disease resistance.
- Benefits: Reduces mortality by 15-20%, improves FCR by 10%, and protects shrimp from vibriosis.
- Implementation: Spray-coated during extrusion, sourced from BioMar.
- Cost: $50/ton.
- Prebiotics:
- Description: Inulin and mannanoligosaccharides (MOS) from sugarcane byproducts (1-2% inclusion).
- Benefits: Boosts probiotic efficacy, improves digestion, cuts feed costs by 5%.
- Implementation: Blended during mixing, sourced locally.
- Cost: $20/ton.
- Clear Water Microbiology:
- Description: Nitrosomonas, Nitrobacter, and Bacillus spp. reduce ammonia/nitrite by 90% in RAS, supporting biofloc.
- Benefits: Eliminates water exchange, reduces feed costs by 10% via biofloc.
- Implementation: Produced in on-site bioreactors, co-developed with AquaBioTech Group.
- Cost: $0.6M/year.
Proprietary Technologies
- BSF Rearing Modules: Process 3,000 tons/year of waste into 1,500 tons of larvae, co-developed with EntoFarm Solutions.
- Silkworm Processing: Automated drying/grinding systems, integrated with sericulture.
- Algae Bioreactors: 10-hectare hybrid pond-photobioreactor system for Spirulina, Schizochytrium, and Chlorella, co-developed with AlgaeTech.
- Cassava Fermentation Units: On-site bioreactors ferment cassava with microbial cultures, enhancing digestibility.
- Feed Extrusion: Bühler Group extruders with probiotic coating, achieving FCR of 1.14.
- Microbial Bioreactors: Produce probiotic and water microbiology cultures.
- Blockchain Tracking: IBM platform tracks all ingredients, ensuring transparency for ASC/BAP compliance.
Economic Feasibility
The $76 million budget supports a high-capacity facility with enhanced ROI.
- Capital Expenditure (CapEx):
- Land and site preparation: $7 million
- Feed manufacturing plant: $20 million
- BSF rearing modules: $10 million
- Algae bioreactors and ponds: $11 million (expanded for Chlorella)
- Silkworm processing and storage: $5 million
- Microbial bioreactors and dosing systems: $5 million
- Cassava fermentation units: $1 million
- Blockchain and IoT systems: $4 million
- Training, permits, miscellaneous: $2 million
- Contingency (20%): $11 million
- Total CapEx: $76 million
- Operational Expenditure (OpEx):
- Raw materials: $124 million/year (includes moringa, Chlorella, yeast hydrolysate)
- Probiotics/prebiotics/microbial cultures: $3 million/year
- Labor: $4 million/year (160 staff)
- Energy: $2 million/year (1 MW solar offsets 50%)
- Maintenance and blockchain: $2 million/year
- Total OpEx: $135 million/year
- Revenue Projections:
- Production: 150,000 tons (120,000 tons tilapia feed, 30,000 tons shrimp feed)
- Selling price: $2,000/ton (tilapia), $2,400/ton (shrimp), premium for enhanced feed
- Export revenue: 100,000 tons (80,000 tons tilapia, 20,000 tons shrimp) = $160M (tilapia) + $60M (shrimp) = $220M
- Internal use: 50,000 tons saves $4M/year vs. market prices
- Total Revenue: $224 million/year
- Return on Investment (ROI):
- Net profit: $224M – $135M = $89 million/year
- ROI: ($89M / $76M) × 100 = 1% annually
- Payback period: ~0.85 years
- Economic Benefits for the Dominican Republic:
- Job Creation: 160 direct jobs (operators, technicians, microbiologists, IT) and 650 indirect jobs (cassava farming, moringa cultivation, logistics).
- Export Revenue: $220 million/year, boosting foreign exchange.
- Local Economy: Stimulates cassava, moringa, and brewery byproduct industries.
- Farm Synergy: Saves $4M/year in feed costs.
Efficient Labor Utilization
- Automation: Automated BSF rearing, algae harvesting, cassava fermentation, and extrusion reduce labor by 40%.
- Training: Partnerships with UASD and INTEC train workers in advanced technologies.
- Scalability: Modular systems support flexible staffing.
Environmental Benefits
- Waste Reduction: BSF converts 3,000 tons/year of waste; cassava and yeast hydrolysate utilize byproducts.
- Water Treatment: Algae and microbiology treat 1.5 million gallons/year of wastewater.
- Low Carbon Footprint: Solar and waste-based inputs cut emissions by 60%.
- Sustainable Sourcing: Eliminates fishmeal/fish oil, preserving marine ecosystems.
- Healthier Aquaculture: Probiotics and yeast hydrolysate reduce antibiotic use by 80%.
- Transparency: Blockchain verifies sustainability, meeting export standards.
Integration with Tilapia and Shrimp Farm
- Cost Reduction: Supplies 50,000 tons at $1,400/ton (tilapia) and $1,650/ton (shrimp), saving $4M/year.
- Sustainability: Enhanced feed and microbiology align with farm’s zero-discharge RAS.
- Export Synergy: Shared warehouse and blockchain streamline feed and seafood exports.
Export Strategy
- Target Markets: USA (50%), Brazil (20%), Mexico (15%), Caribbean (15%).
- Competitive Advantage: Nutrient-dense, probiotic-enhanced, blockchain-tracked feed meets ASC/BAP standards.
- Logistics: DR-CAFTA ensures low tariffs; ports facilitate efficient shipping.
- Marketing: Highlight moringa minerals, Chlorella sustainability, and yeast hydrolysate health benefits via blockchain app.
Implementation Plan
- Phase 1 (Year 1): Site expansion, permitting, construction of plant, BSF, algae, and cassava units. Budget: $40 million.
- Phase 2 (Year 2): Install silkworm processing, microbial bioreactors, blockchain, and begin production. Budget: $25 million.
- Phase 3 (Year 3): Full-scale production, export operations, and farm integration. Budget: $11 million.
- Phase 4 (Years 4-5): Scale to 300,000 tons/year, expanding market reach.
Risks and Mitigation
- Risk: High CapEx. Mitigation: Phased implementation, grants (FAO, NOAA), partner funding.
- Risk: Export competition. Mitigation: Premium pricing for enhanced feed.
- Risk: Raw material supply. Mitigation: Diversify cassava, moringa, and soybean sources.
- Risk: Energy costs. Mitigation: 1 MW solar array and battery storage.
Conclusion
Geodyn Solutions’ $76 million enhanced feed facility leverages BSF, silkworm pupae, algae, soybean meal, fermented cassava, moringa, yeast hydrolysate, probiotics, prebiotics, and microbiology to produce 150,000 tons of premium feed. With a 117.1% ROI, 810 jobs, and $220 million in export revenue, it positions the Dominican Republic as a global aquaculture feed leader, driving economic growth and sustainability.
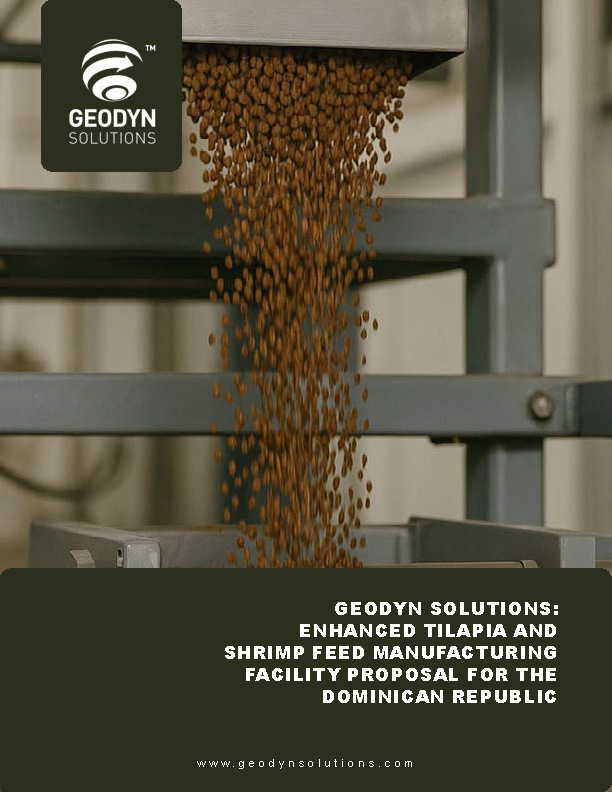
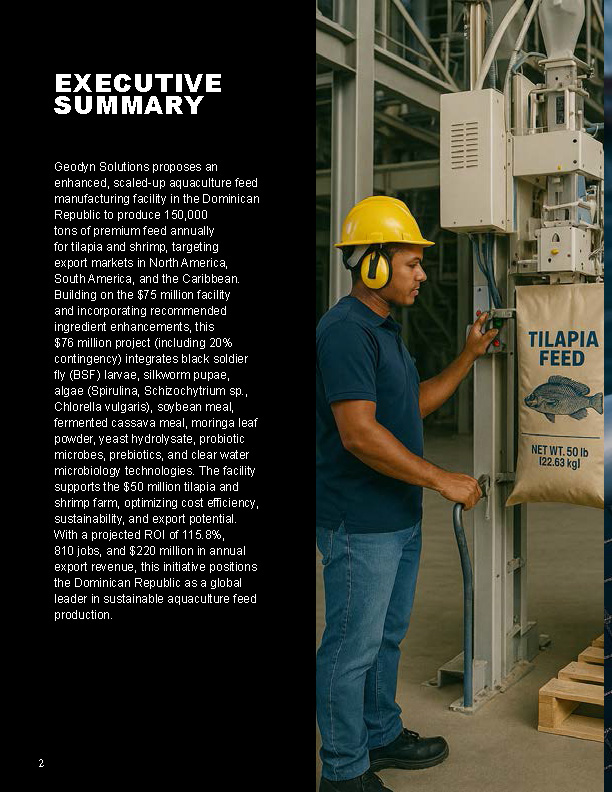
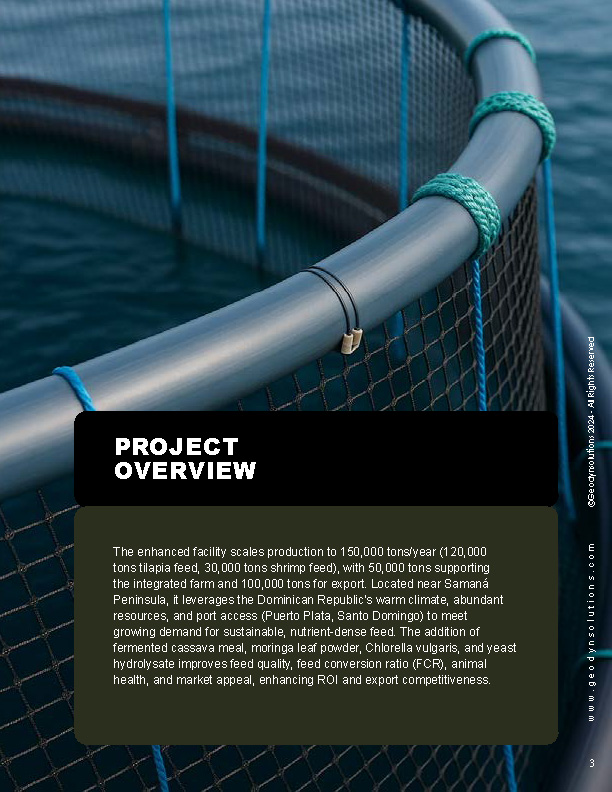
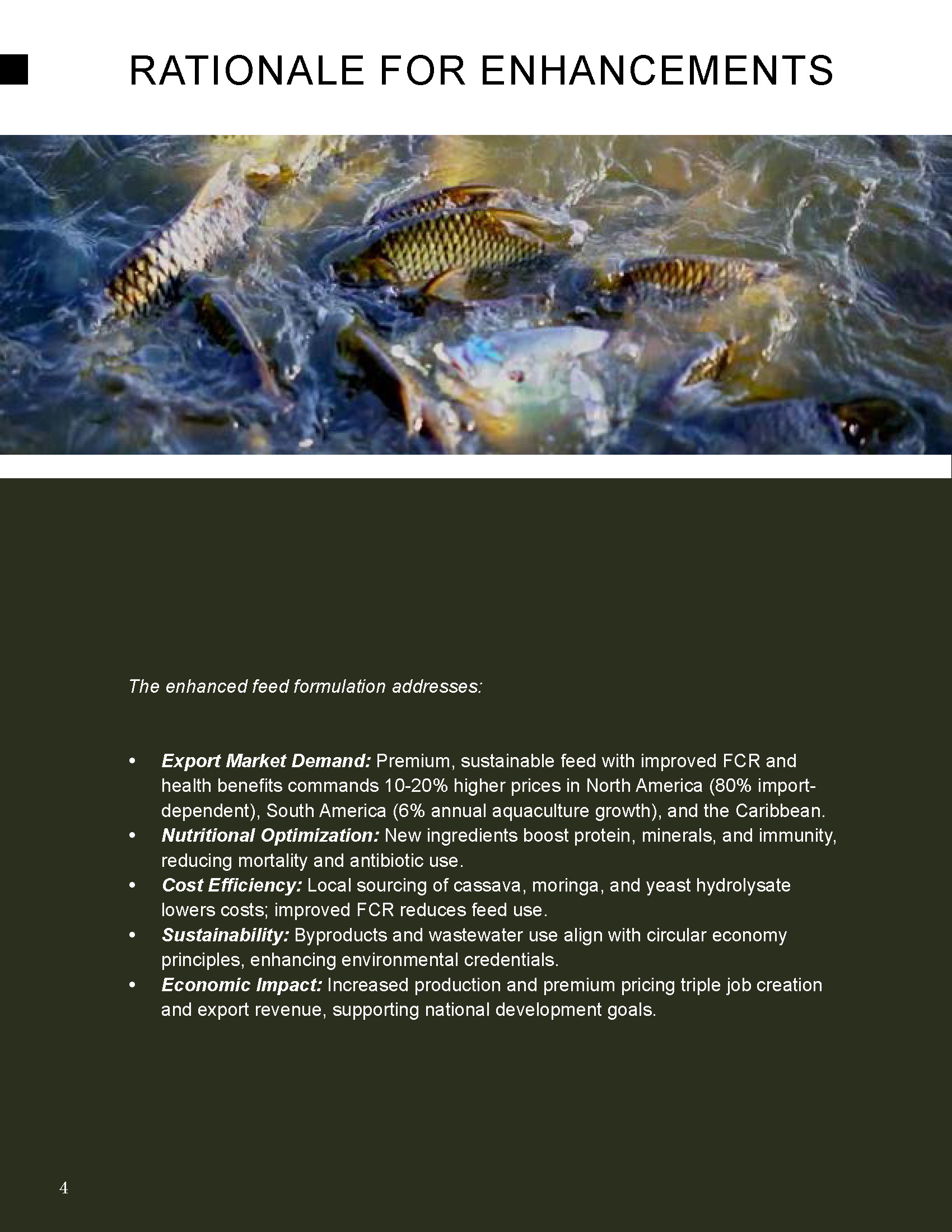
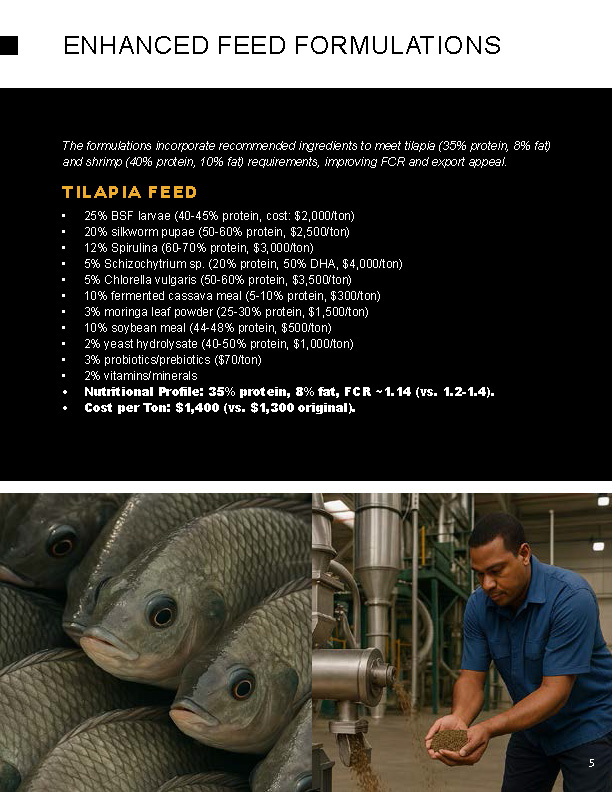
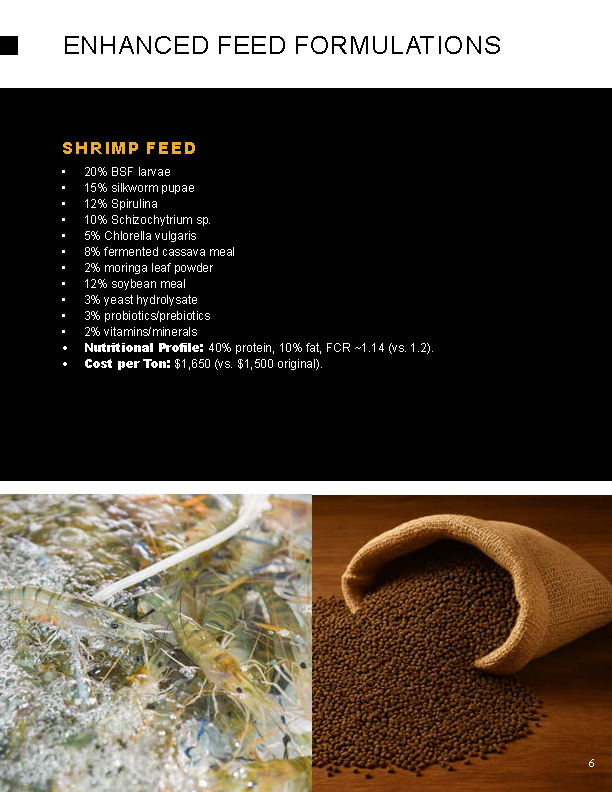
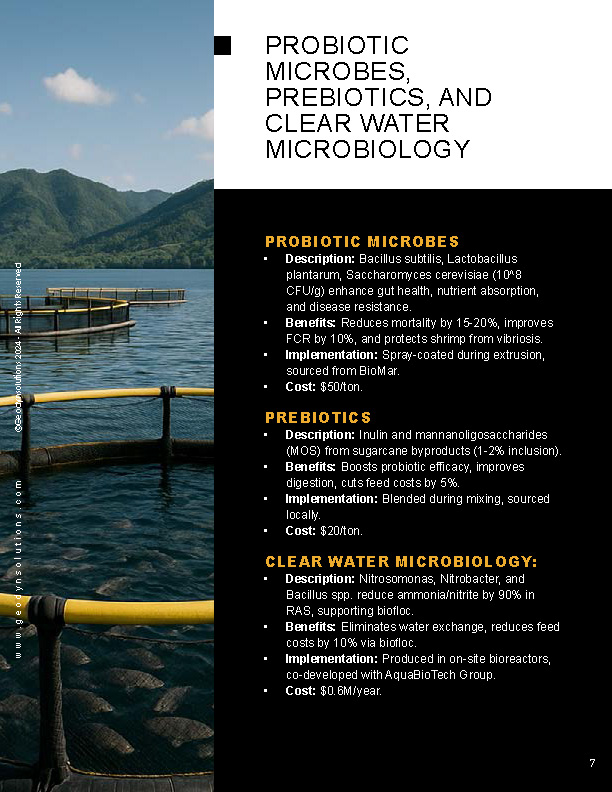
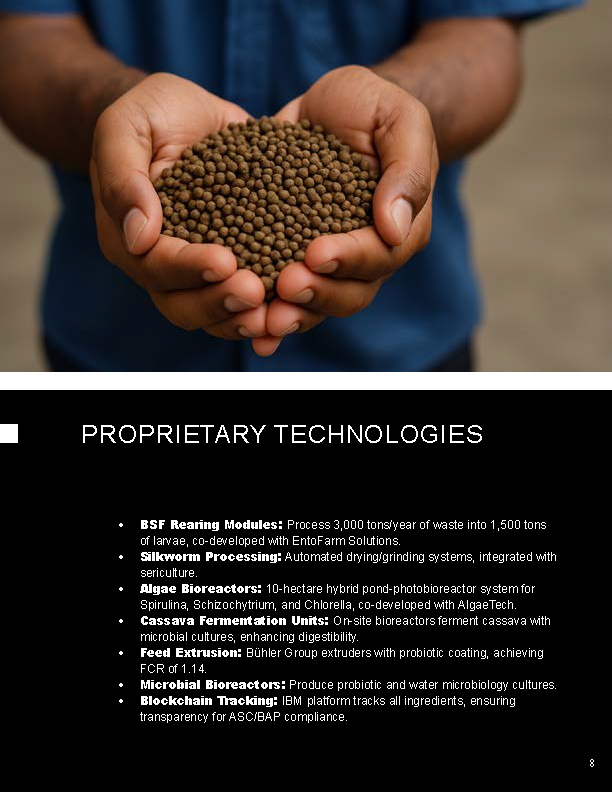
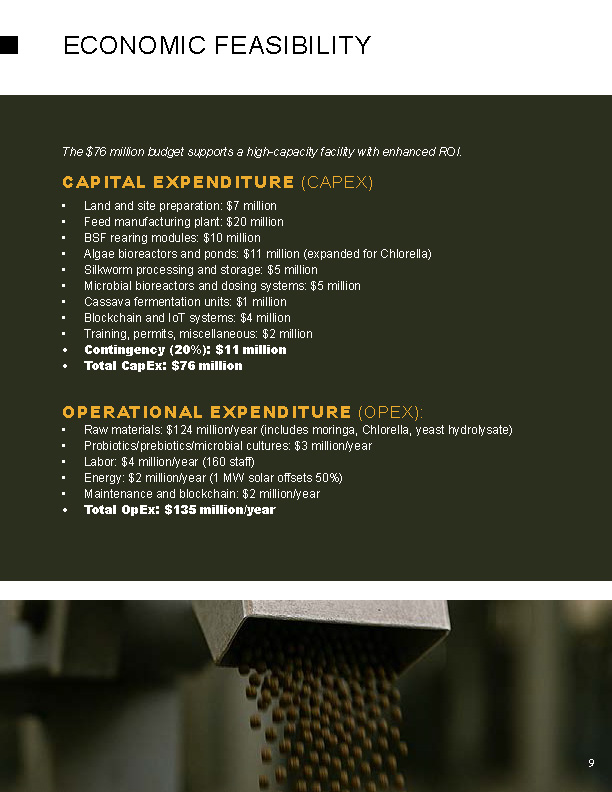
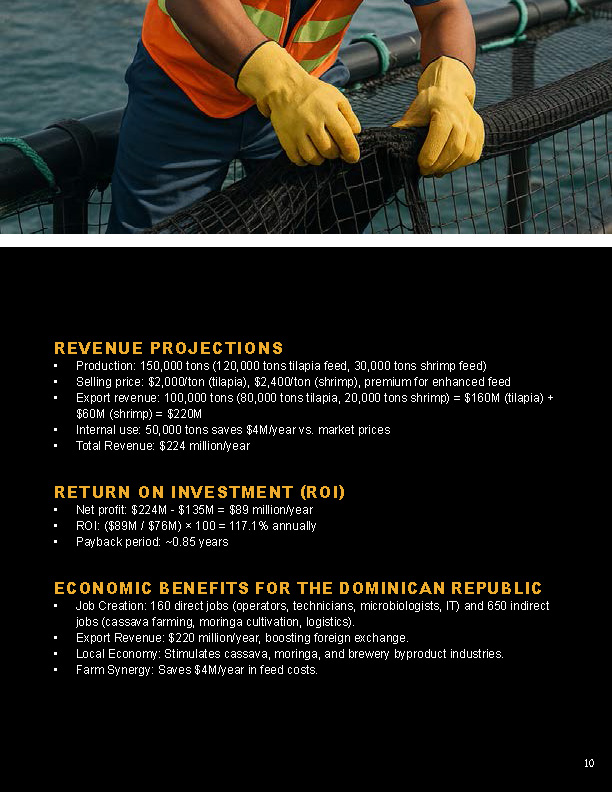
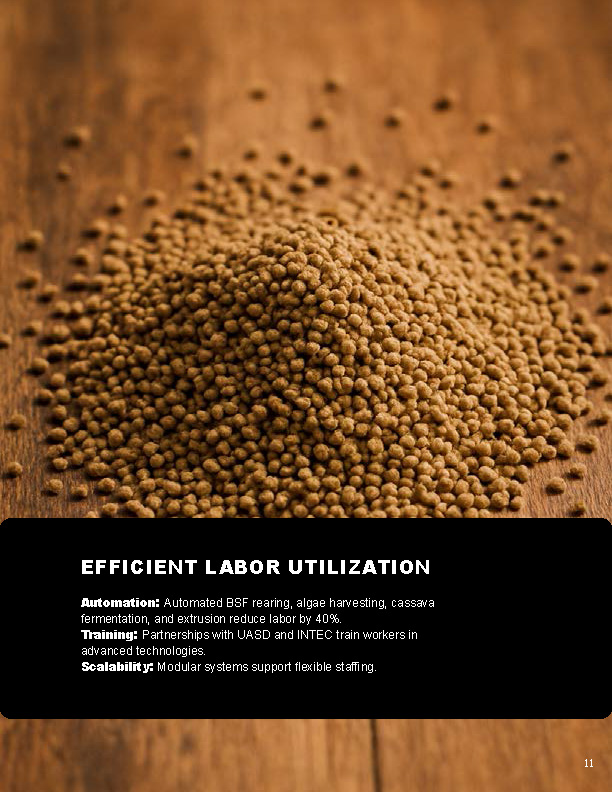
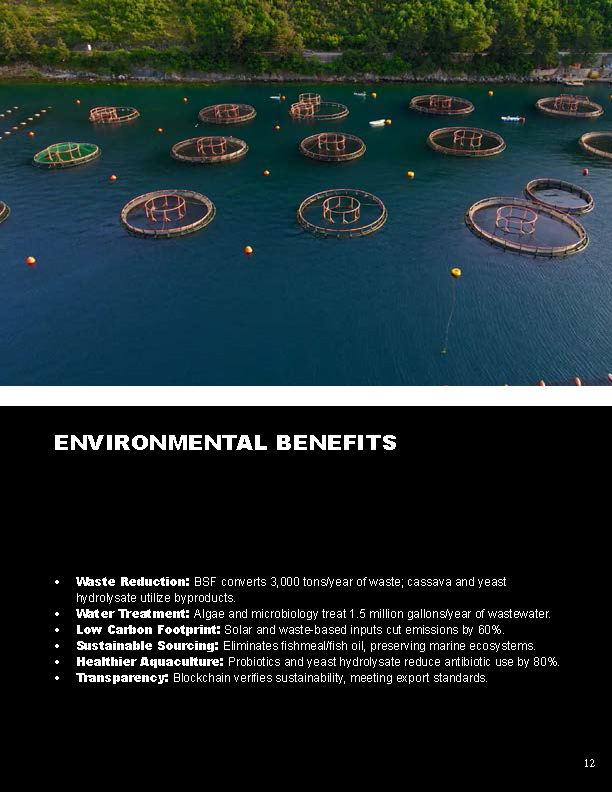
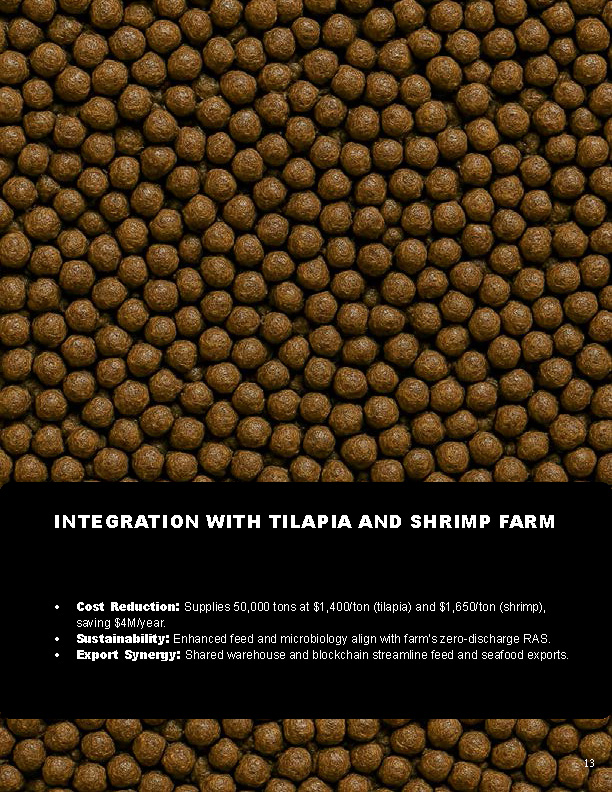
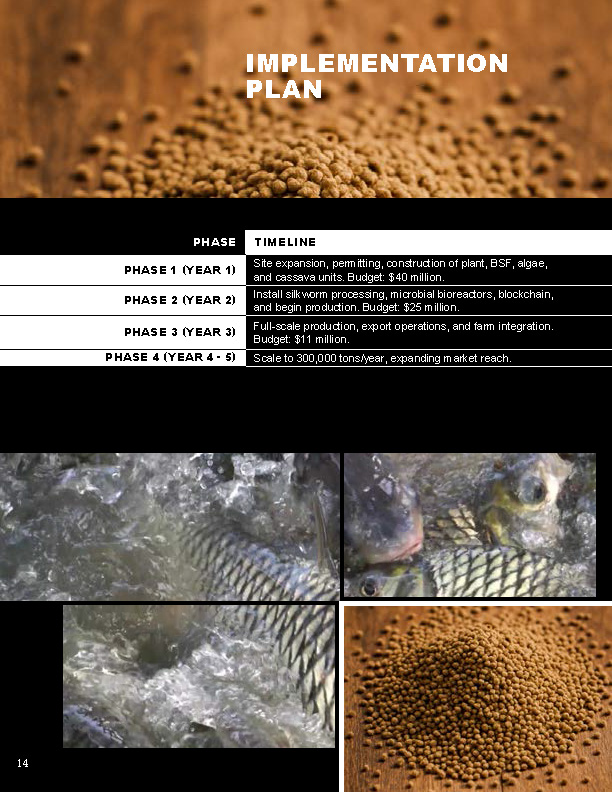
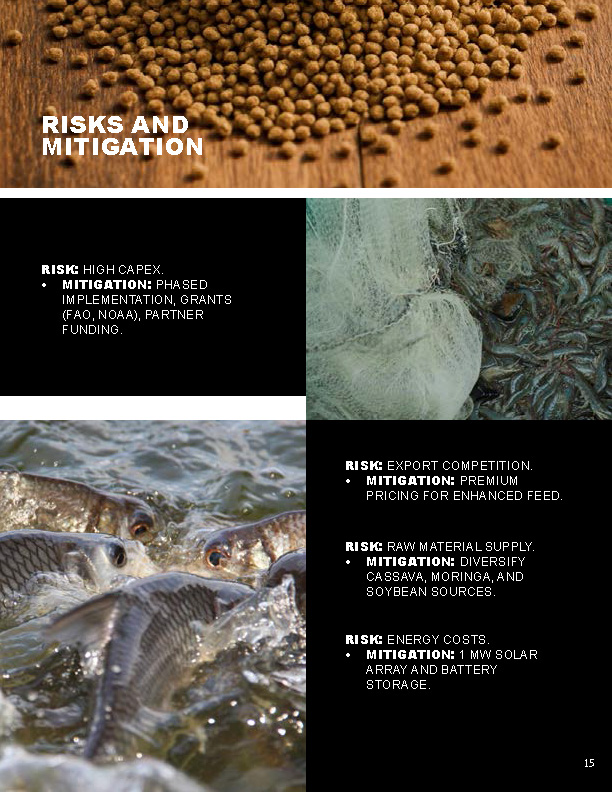
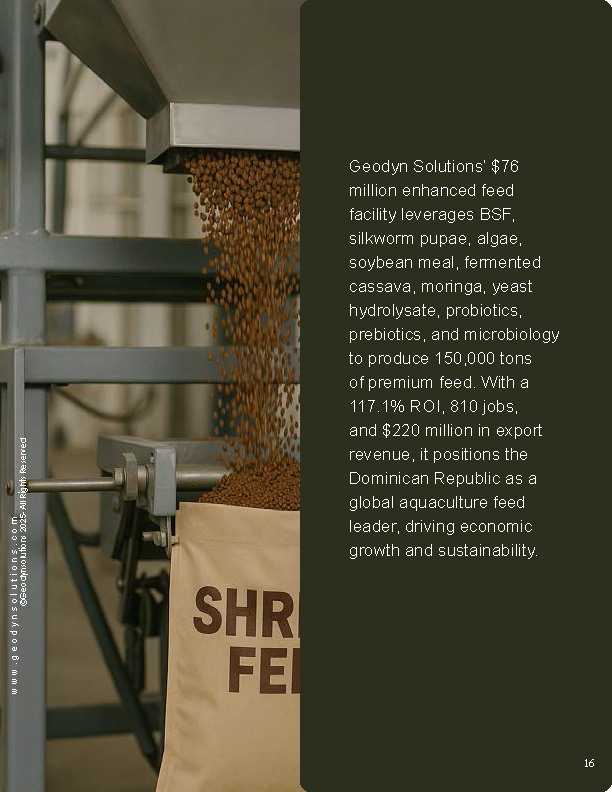
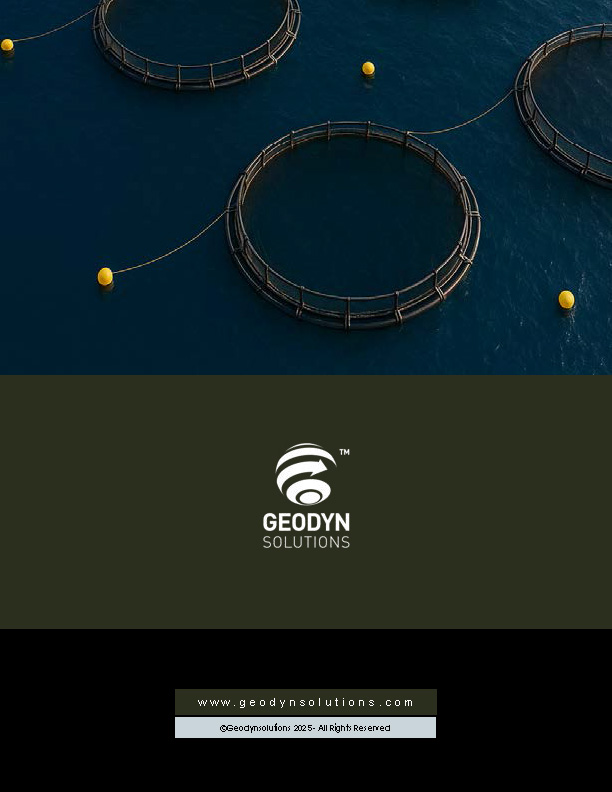